Our Company
Rotomolding Innovative Proprietary Products Since 2017
Founded by experts in the rotomolding industry, TRI-VEN was formed to meet the needs of growing partnerships by manufacturing top-quality proprietary products for those brands. TRI-VEN delivers on this mission through rotational molding, a process that adds outstanding consistency, strength and durability to the final product. From our products to our people, you can rely on TRI-VEN to be the best possible partner for you, your customers and your team.
Industry Expertise
Our diverse portfolio of products manufactured exclusively for our partners makes TRI-VEN unique in the rotomolding industry.. Our partners benefit from our vast knowledge base of rotomolding’s strengths and capabilities as well as our wide-ranging expertise manufacturing products for many different industries and applications.
Prioritizing People
At TRI-VEN, we know our people are our greatest asset. We strive to be worthy of our employees’ commitment, skill and experience by building a family-style workplace culture on a foundation of teamwork, mutual respect, and a meaningful investment in professional development.
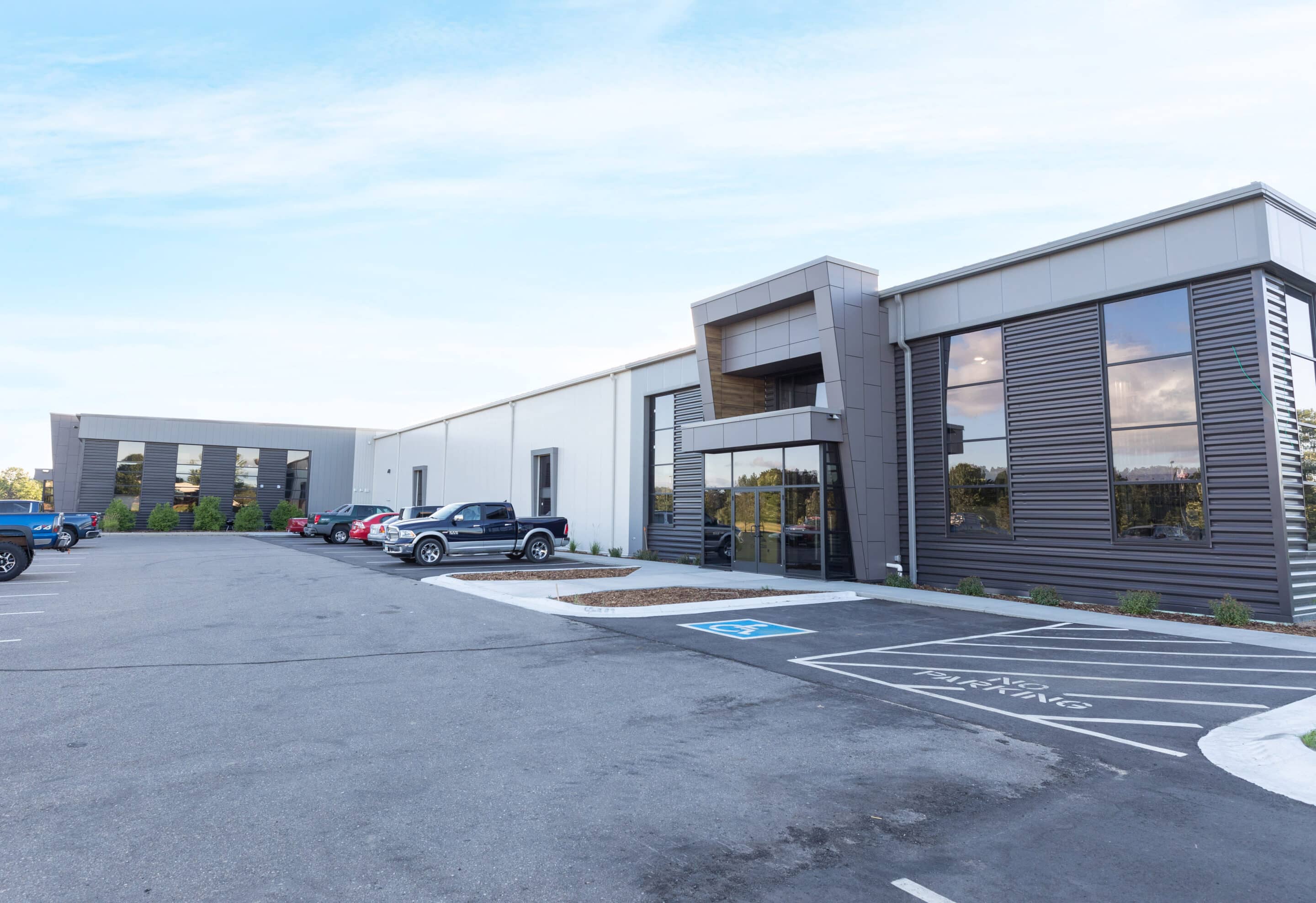
Our Process
The Molds
Our sister company Avantech first designs and manufactures molds to match the geometry of the finished product we will be rotomolding. Avantech’s ability to produce extreme-tolerance molds allows us to hold tighter tolerances in the rotomolding process, resulting in finished goods of outstanding quality.
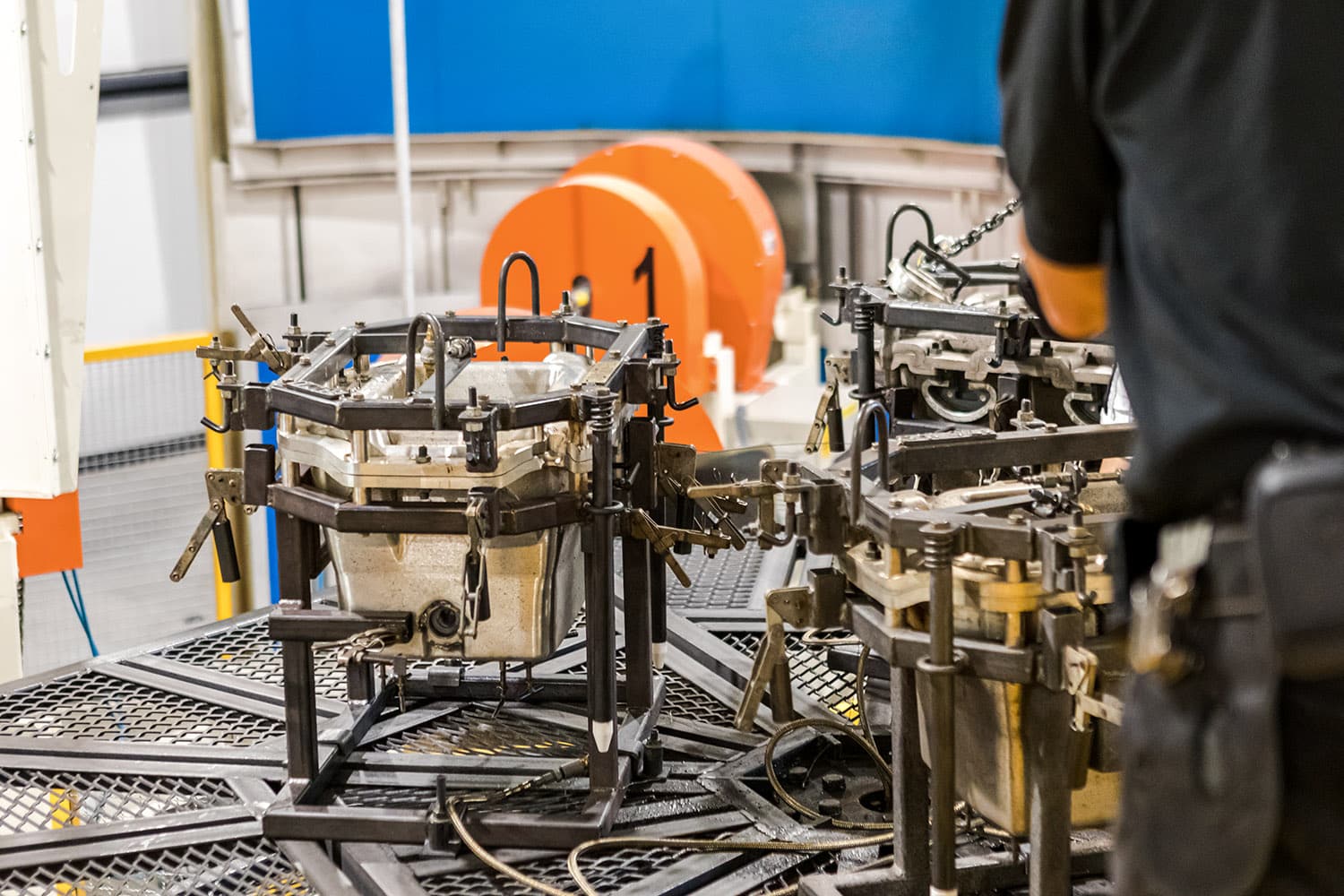
The Raw Materials
Polyethylene is the most common type of plastic used in the rotational molding industry. Because of its versatility, TRI-VEN produces the majority of partnership products with it; however, TRI-VEN also has the capability and experience of rotomolding polypropylene, a material widely used for high-heat applications. These materials are delivered to TRI-VEN in powder form with a consistency comparable to sugar sand. This powder-like plastic is poured into the molds, heated and shaped using the rotomolding process.
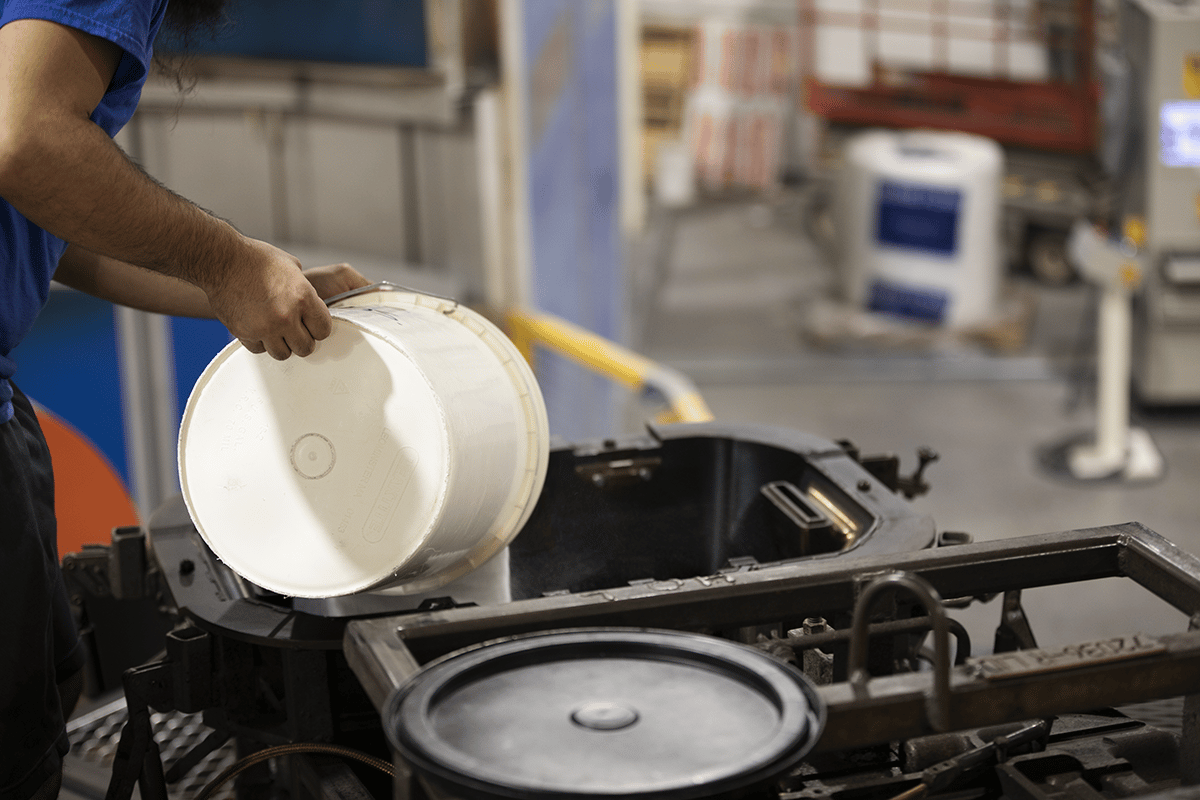
The Machinery
The versatility of our partners drives the versatility of our equipment. With products that range in scale from the size of a single step-stool to that of a double bed frame, our machinery is sized accordingly to efficiently and effectively produce products of all sizes.
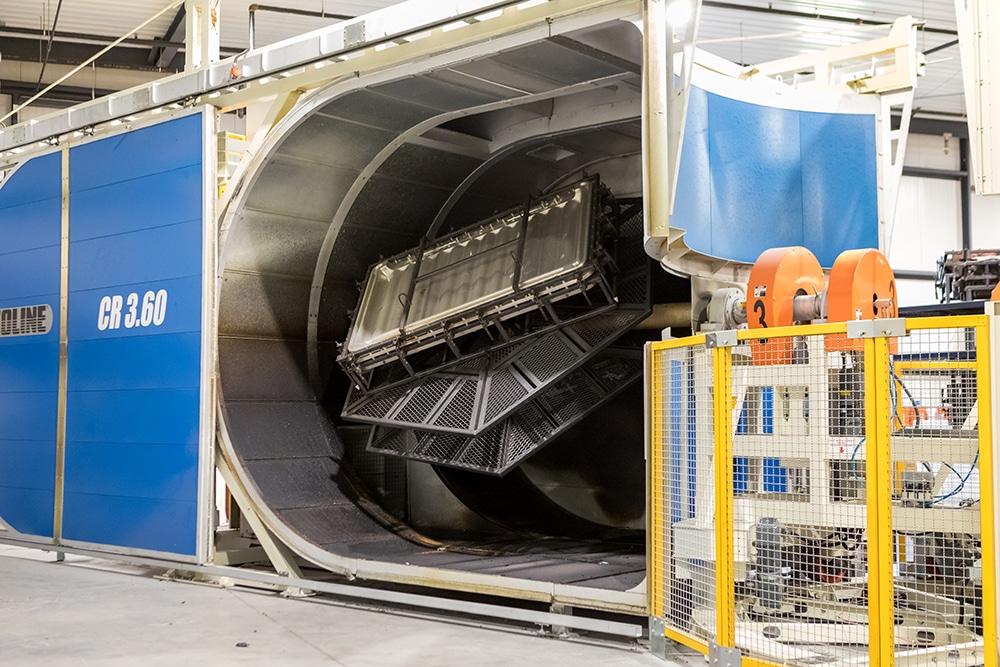
The Process
The plastic resin inside the mold is heated to a liquid form within the roto-machine while simultaneously spinning on a five-axis arm. The spinning motion creates the remarkably consistent plastic wall thickness for which the rotomolding process is known.
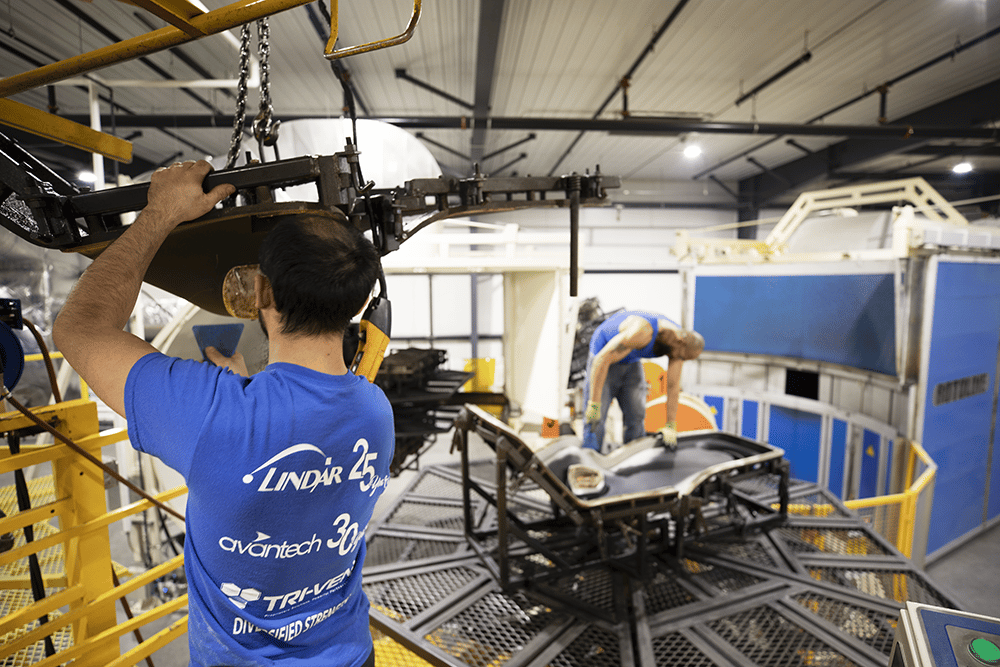
The Finishing Touches
When the rotomolding process has completed, the product is removed from the machine and mold and allowed to cool. Once cooled, the product is then trimmed and assembled before going through a comprehensive quality check.
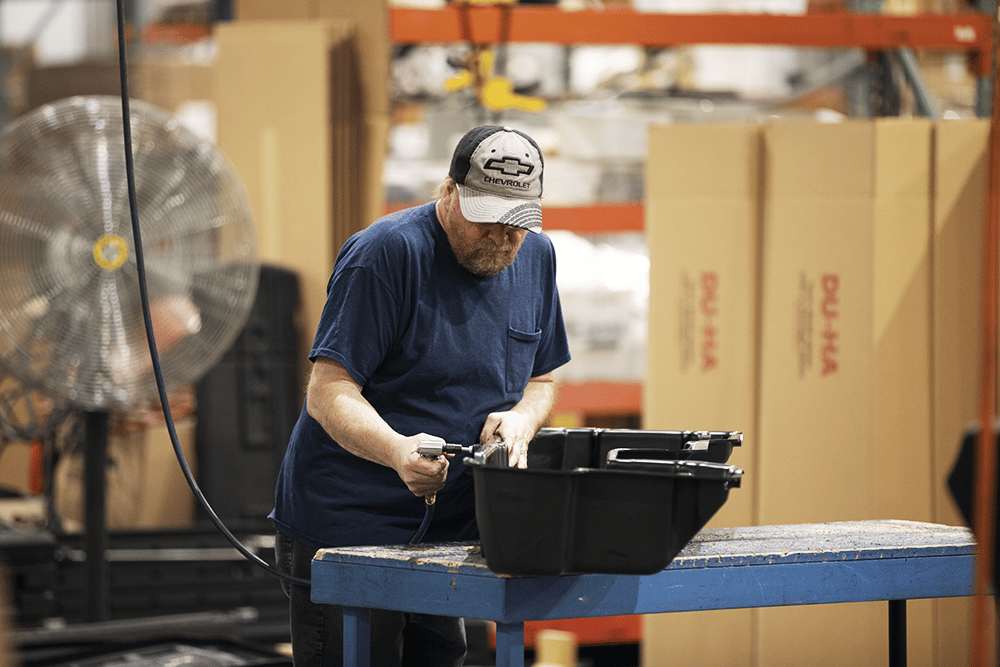
Shipping
Following a successful quality check, the product is securely packaged and prepared to ship anywhere in the world. Our team takes great care to ensure products arrive intact and ready to perform.
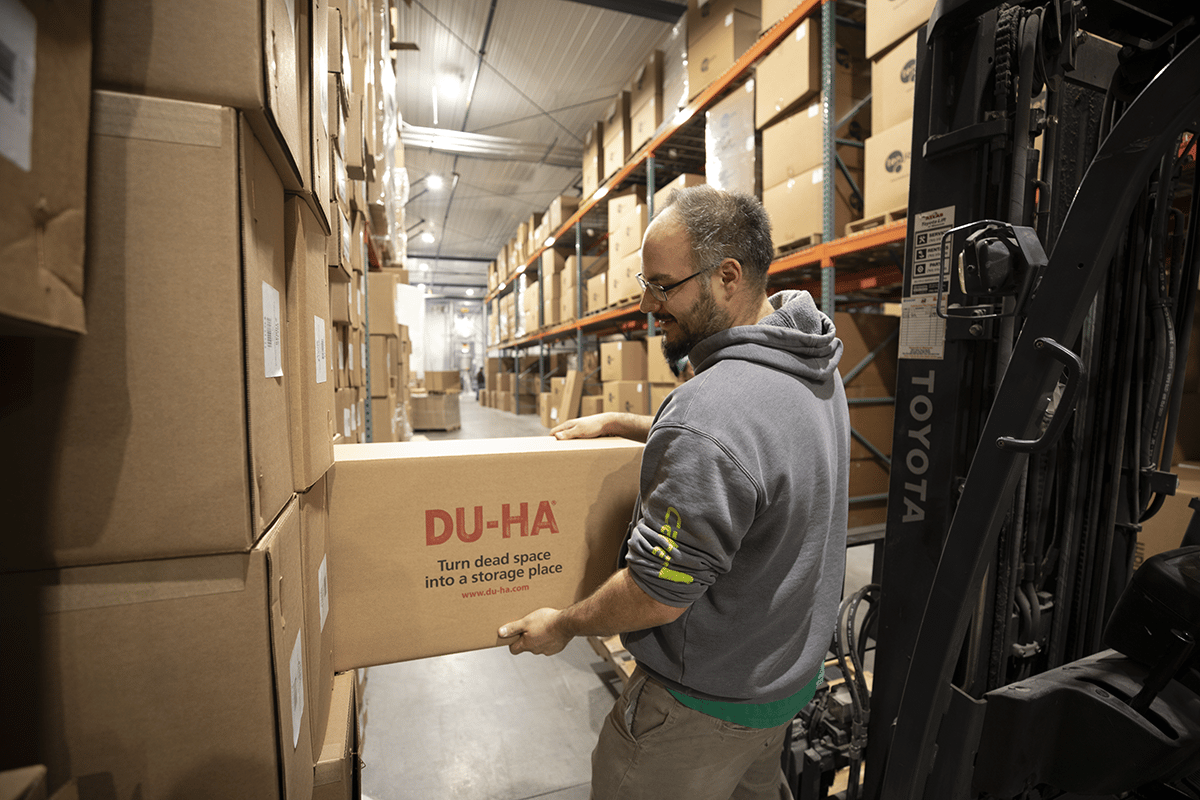
The Molds
Our sister company Avantech first designs and manufactures molds to match the geometry of the finished product we will be rotomolding. Avantech’s ability to produce extreme-tolerance molds allows us to hold tighter tolerances in the rotomolding process, resulting in finished goods of outstanding quality.
The Raw Materials
Polyethylene is the most common type of plastic used in the rotational molding industry. Because of its versatility, TRI-VEN produces the majority of partnership products with it; however, TRI-VEN also has the capability and experience of rotomolding polypropylene, a material widely used for high-heat applications. These materials are delivered to TRI-VEN in powder form with a consistency comparable to sugar sand. This powder-like plastic is poured into the molds, heated, and shaped using the rotomolding process.
The Machinery
The versatility of our partners drives the versatility of our equipment. With products that range in scale from the size of a single step-stool to that of a double bed frame, our machinery is sized accordingly to efficiently and effectively produce products of all sizes.
The Process
The resin inside the mold is heated to a liquid form within the roto-machine while simultaneously spinning on a five-axis arm. The spinning motion creates the remarkably consistent plastic wall thickness for which the rotomolding process is known.
The Finishing Touches
When the rotomolding process has completed, the product is removed from the machine and mold and allowed to cool. Once cooled, the product is then trimmed and assembled before going through a comprehensive quality check.
Shipping
Following a successful quality check, the product is securely packaged and prepared to ship anywhere in the world. Our team takes great care to ensure products arrive intact and ready to perform.
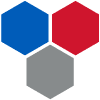